Top 5 Tips for Using Telematics to Maintain a MEWP Fleet

by Christine Zeznick - Director of Product and Business Development On Mar 19, 2020, 03:00 AM
Subscribe To Aerial Pros
Filter by tags
Increased market competition and competitive rental rates are significant challenges for rental companies. One of the ways rental companies are staying ahead of their competition is to adopt new technologies.
Driving today’s machine technology changes is the need to increase productivity, as well as increase fleet utilization and management. A tool that many rental companies now use to manage their mobile elevating work platform (MEWP) fleets is telematics, which can provide insights on everything from tracking machine location to proactively scheduling machine maintenance and optimizing equipment utilization.
Here are five tips for using a telematics programme to help maintain a MEWP rental fleet:
Tip #1: Telematics programmes should focus providing information that allows equipment owners to take action.
No matter what size of aerial equipment fleet — from 10 to 10,000 machines — equipment management is something that rental stores do every day. Data is great, but value is created when data is transformed into actionable information. From knowing how equipment is performing or how often a piece is being utilized to where each unit is or when it is ready for maintenance, machine data can provide a lot of insight to rental businesses.
With dashboards and alert notifications, telematics can help rental fleet managers understand the information their machines are providing, enabling them to not only react to what is currently going on with their equipment but also to proactively manage what will be happening with their fleet.
Tip #2: Telematics can play a vital role in effectively putting rental stores in the position to proactively manage a machine’s uptime — scheduling maintenance when it is needed, based on usage and not the calendar.
With telematics, rental stores can know:
- When was the last scheduled maintenance? Is it due for another?
- How many hours are on the machine?
- How long is the machine being used for per day?
- How many hours has the engine run on this particular rental?
Knowing the answers to these questions means that telematics will change the way the machines are serviced. Telematics can also help rental stores schedule preventive maintenance needs, based on tracking hours remotely, which can translate to big savings because customers can proactively perform these tasks, even during a long-term rental.
Tip #3: Telematics can help alleviate a major challenge in the industry today that there aren’t enough service technicians in our industry.
Telematics programme offers “descriptive” data, allowing rental companies know what’s going on with the machine. When a key user the rental house sees a critical fault code, for example, he/she can analyze the need and contact the customer to proactively discuss troubleshooting, saving expensive machine transport back to the yard and valuable service technicians’ travel time.
Think about it this way — descriptive data answers today’s question: “What is happening?”
- Hours
- Location
- Machine idle time
- Faults
Tip #4: Telematics can also help with remote troubleshooting equipment issues in the field
What this means is if a MEWP operator has a problem with a machine in the field, rental stores can use the information provided through telematics to potentially identify the issue and potentially any parts required, before sending a technician out, which saves time and money.
Utilizing telematics for remote troubleshooting gives rental fleet managers the ability to help track equipment and proactively respond to equipment issues in the field, which can make the difference for both securing the rental, as well as forging stronger relationships with customers.
Tip #5: Data from telematics can be leveraged on a larger scale and be used for “predictive” and “prescriptive” activities, such as predicting failures in the field based on how the equipment is actually being used and proactively prescribing maintenance and service.
To understand this, predictive data answers tomorrow’s question: “What will happen?”
- Predict failures before they occur
- An example would be predicting battery or charger failure for replacement before actual downtime occurs
And, prescriptive data answers the question: “What do I need to do?”
- Recommend action to be taken
- An example would be knowing that the machine needs to be serviced now because of the way it’s being used, and then schedule to perform maintenance on another machine of the same type later because of its usage pattern
Technology continues to transform the rental industry — and today, rental stores have tools, like telematics, at their disposal to run their business more efficiently and more profitably than ever before.
Related Posts

It’s Time to Embrace Telematics — Here’s Why
From reading about it in countless articles within trade magazines to conversations with peers, it’s easy to understand that telematics can bring a lot of benefits to rental businesses.
Continue Reading
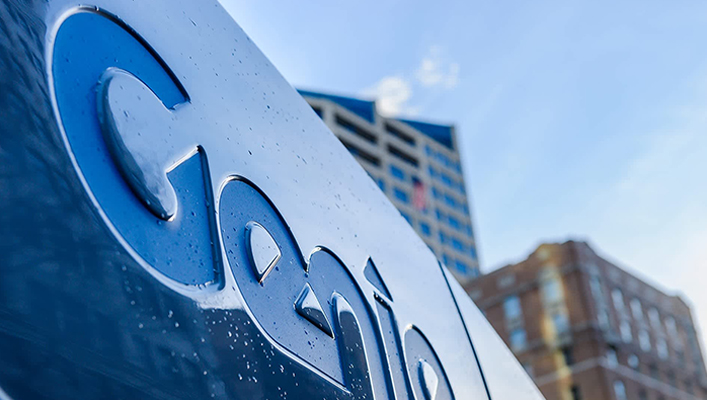
Telematics and the Data Sharing Economy
As the construction industry continues to modernize its business operation, telematics technology is now being widely adopted and more commonly used in the aerial rental market.
Continue Reading

How Machine Data Influences MEWP Maintenance and Service
When looking at a machine’s service and repair from that perspective, downtime costs a rental business big time.
Continue Reading